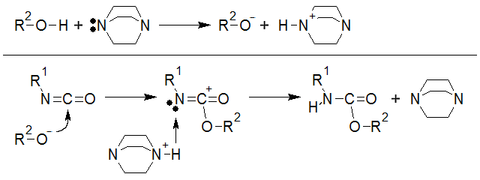
1, indice d'hydroxyle : 1 gramme de polyol polymère contenait une quantité d'hydroxyle (-OH) équivalente au nombre de milligrammes de KOH, l'unité mgKOH/g.
2, équivalent : le poids moléculaire moyen d'un groupe fonctionnel.
3, teneur en isocyanate : la teneur en isocyanate dans la molécule
4, Indice isocyanate : indique le degré d'excès d'isocyanate dans la formule polyuréthane, généralement représenté par la lettre R.
5. Prolongateur de chaîne : il fait référence aux alcools et aux amines de faible poids moléculaire qui peuvent étendre, étendre ou former des réticulations de réseaux spatiaux de chaînes moléculaires.
6. Segment dur : Le segment de chaîne formé par la réaction de l'isocyanate, de l'extenseur de chaîne et de l'agent de réticulation sur la chaîne principale des molécules de polyuréthane, et ces groupes ont une plus grande énergie de cohésion, un plus grand volume spatial et une plus grande rigidité.
7, segment souple : polyol polymère de chaîne principale de carbone carbone, la flexibilité est bonne, dans la chaîne principale de polyuréthane pour le segment de chaîne flexible.
8, méthode en une étape : fait référence au polyol oligomère, au diisocyanate, à l'extenseur de chaîne et au catalyseur mélangés en même temps après injection directe dans le moule, à une certaine méthode de moulage de durcissement à température.
9, méthode prépolymère : première réaction de prépolymérisation du polyol oligomère et du diisocyanate, pour générer un prépolymère de polyuréthane à base de NCO final, coulée puis réaction du prépolymère avec un prolongateur de chaîne, méthode de préparation de l'élastomère polyuréthane, appelée méthode du prépolymère.
10, Méthode semi-prépolymère : la différence entre la méthode semi-prépolymère et la méthode prépolymère est qu'une partie du polyester polyol ou du polyéther polyol est ajoutée au prépolymère sous la forme d'un mélange avec un extenseur de chaîne, un catalyseur, etc.
11, moulage par injection de réaction : également connu sous le nom de moulage par injection de réaction RIM (moulage par injection de réaction), il est mesuré par des oligomères de faible poids moléculaire sous forme liquide, instantanément mélangés et injectés dans le moule en même temps, et la réaction rapide dans le cavité du moule, le poids moléculaire du matériau augmente rapidement. Un procédé permettant de générer des polymères entièrement nouveaux avec de nouvelles structures de groupes caractéristiques à des vitesses extrêmement élevées.
12, Indice de moussage : c'est-à-dire que le nombre de parties d'eau utilisées dans 100 parties de polyéther est défini comme indice de moussage (IF).
13, Réaction moussante : fait généralement référence à la réaction de l'eau et de l'isocyanate pour produire de l'urée substituée et libérer du CO2.
14, Réaction de gel : fait généralement référence à la formation d’une réaction de carbamate.
15, temps de gel : dans certaines conditions, le matériau liquide pour former le gel a nécessité du temps.
16, Temps laiteux : à la fin de la zone I, un phénomène laiteux apparaît dans le mélange polyuréthane en phase liquide. Ce temps est appelé temps de crème dans la génération de mousse polyuréthane.
17, Coefficient d'expansion de chaîne : fait référence au rapport entre la quantité de groupes amino et hydroxyle (unité : mo1) dans les composants d'extension de chaîne (y compris l'extension de chaîne mixte) et la quantité de NCO dans le prépolymère, c'est-à-dire le nombre de moles. (nombre équivalent) rapport du groupe hydrogène actif au NCO.
18, polyéther à faible insaturation : principalement pour le développement du PTMG, prix PPG, insaturation réduite à 0,05 mol/kg, proche des performances du PTMG, utilisant un catalyseur DMC, la principale variété de produits de la série Bayer Acclaim.
19, Solvant de qualité ester d'ammoniac : la production de solvant de polyuréthane pour prendre en compte la force de dissolution, le taux de volatilisation, mais la production de polyuréthane utilisé dans le solvant devrait se concentrer sur la prise en compte du NC0 lourd dans le polyuréthane. Les solvants tels que les alcools et les étheralcools qui réagissent avec les groupes NCO ne peuvent pas être sélectionnés. Le solvant ne peut pas contenir d'impuretés telles que l'eau et l'alcool, ni de substances alcalines, ce qui détériorerait le polyuréthane.
Le solvant ester ne doit pas contenir d'eau et ne doit pas contenir d'acides libres ni d'alcools, qui réagiraient avec les groupes NCO. Le solvant ester utilisé dans le polyuréthane doit être un « solvant de qualité ester d’ammoniac » de haute pureté. C'est-à-dire que le solvant réagit avec un excès d'isocyanate, puis la quantité d'isocyanate n'ayant pas réagi est déterminée avec de la dibutylamine pour tester s'il convient à son utilisation. Le principe est que la consommation d'isocyanate n'est pas applicable, car elle montre que l'eau contenue dans l'ester, l'alcool, l'acide trois consommera la valeur totale de l'isocyanate, si le nombre de grammes de solvant nécessaire pour consommer le groupe leqNCO est exprimé, le la valeur est une bonne stabilité.
Un équivalent isocyanate inférieur à 2 500 n’est pas utilisé comme solvant polyuréthane.
La polarité du solvant a une grande influence sur la réaction de formation de résine. Plus la polarité est grande, plus la réaction est lente, comme la différence de toluène et de méthyléthylcétone de 24 fois, cette polarité de molécule de solvant est grande, peut former une liaison hydrogène avec le groupe hydroxyle de l'alcool et ralentir la réaction.
Il est préférable de choisir un solvant ester polychloré, un solvant aromatique, sa vitesse de réaction est plus rapide que celle des esters, cétones, tels que le xylène. L'utilisation de solvants esters et cétoniques peut prolonger la durée de vie du polyuréthane double branche pendant la construction. Dans la production de revêtements, le choix du « solvant de qualité ammoniac » mentionné précédemment est bénéfique pour les stabilisants stockés.
Les solvants esters ont une forte solubilité, un taux de volatilisation modéré, une faible toxicité et sont davantage utilisés, la cyclohexanone est également davantage utilisée, les solvants hydrocarbonés ont une faible capacité de dissolution des solides, moins utilisés seuls et davantage avec d'autres solvants.
20, Agent gonflant physique : l'agent gonflant physique est que les pores de la mousse se forment par le changement de la forme physique d'une substance, c'est-à-dire par l'expansion du gaz comprimé, la volatilisation du liquide ou la dissolution du solide.
21, Agents gonflants chimiques : les agents gonflants chimiques sont ceux qui peuvent libérer des gaz tels que le dioxyde de carbone et l'azote après décomposition par chauffage et former de fins pores dans la composition polymère du composé.
22, réticulation physique : il y a des chaînes dures dans la chaîne molle du polymère, et la chaîne dure a les mêmes propriétés physiques que le caoutchouc vulcanisé après réticulation chimique à une température inférieure au point de ramollissement ou au point de fusion.
23, Réticulation chimique : fait référence au processus de liaison de grandes chaînes moléculaires par des liaisons chimiques sous l'action de la lumière, de la chaleur, d'un rayonnement à haute énergie, d'une force mécanique, d'ultrasons et d'agents de réticulation pour former un réseau ou une structure polymère.
24, Indice de moussage : le nombre de parties d'eau équivalentes à 100 parties de polyéther est défini comme indice de moussage (IF).
25. Quels types d'isocyanates sont couramment utilisés en termes de structure ?
A : Aliphatique : HDI, alicyclique : IPDI,HTDI,HMDI, Aromatique : TDI,MDI,PAPI,PPDI,NDI.
26. Quels types d’isocyanates sont couramment utilisés ? Écrire la formule développée
A : Diisocyanate de toluène (TDI), diphénylméthane-4,4'-diisocyanate (MDI), polyphénylméthane polyisocyanate (PAPI), MDI liquéfié, hexaméthylène-diisocyanate (HDI).
27. Signification de TDI-100 et TDI-80 ?
R : TDI-100 est composé de diisocyanate de toluène de structure 2,4 ; TDI-80 fait référence à un mélange composé de 80 % de diisocyanate de toluène de structure 2,4 et de 20 % de structure 2,6.
28. Quelles sont les caractéristiques du TDI et du MDI dans la synthèse des matériaux polyuréthanes ?
A : Réactivité pour le 2,4-TDI et le 2,6-TDI. La réactivité du 2,4-TDI est plusieurs fois supérieure à celle du 2,6-TDI, car le NCO en position 4 dans le 2,4-TDI est loin du NCO en position 2 et du groupe méthyle, et il y a presque pas de résistance stérique, tandis que le NCO du 2,6-TDI est affecté par l'effet stérique du groupe ortho-méthyle.
Les deux groupes NCO du MDI sont éloignés l'un de l'autre et il n'y a aucun substituant autour, donc l'activité des deux NCO est relativement importante. Même si un NCO participe à la réaction, l'activité du NCO restant est diminuée et l'activité reste en général relativement importante. Par conséquent, la réactivité du prépolymère de polyuréthane MDI est supérieure à celle du prépolymère TDI.
29.HDI, IPDI, MDI, TDI, NDI, laquelle des résistances au jaunissement est la meilleure ?
R : HDI (appartient au diisocyanate aliphatique jaune invariant), IPDI (fabriqué en résine polyuréthane avec une bonne stabilité optique et résistance chimique, généralement utilisée pour fabriquer une résine polyuréthane de haute qualité sans décoloration).
30. Objectif de la modification MDI et méthodes de modification communes
A : MDI liquéfié : Objectif modifié : le MDI pur liquéfié est un MDI modifié liquéfié, qui surmonte certains défauts du MDI pur (solide à température ambiante, fondant lors de l'utilisation, chauffage multiple affecte les performances), et constitue également la base d'une large gamme. de modifications pour l'amélioration et l'amélioration des performances des matériaux polyuréthanes à base de MDI.
Méthodes :
① MDI liquéfié modifié à l'uréthane.
② MDI liquéfié modifié par le carbodiimide et l'urétonimine.
31. Quels types de polyols polymères sont couramment utilisés ?
A : polyol de polyester, polyol de polyéther
32. Combien de méthodes de production industrielle existe-t-il pour les polyester-polyols ?
A : Méthode de fusion sous vide B, méthode de fusion du gaz porteur C, méthode de distillation azéotropique
33. Quelles sont les structures particulières du squelette moléculaire des polyesters et des polyéther polyols ?
A : Polyester polyol : Un composé alcoolique macromoléculaire contenant un groupe ester sur le squelette moléculaire et un groupe hydroxyle (-OH) sur le groupe terminal. Polyéther polyols : polymères ou oligomères contenant des liaisons éther (-O-) et des bandes d'extrémité (-Oh) ou des groupes amine (-NH2) dans la structure du squelette de la molécule.
34. Quels sont les types de polyéther polyols selon leurs caractéristiques ?
A : Polyols de polyéther hautement actifs, polyols de polyéther greffés, polyols de polyéther ignifuges, polyols de polyéther modifiés hétérocycliques, polyols de polytétrahydrofurane.
35. Combien de types de polyéthers ordinaires existe-t-il selon l’agent de départ ?
A : Polyoxyde de propylène glycol, polyoxyde de propylène triol, polyéther polyol à bulles dures, polyéther polyol à faible insaturation.
36. Quelle est la différence entre les polyéthers à terminaison hydroxy et les polyéthers à terminaison amine ?
Les polyéthers à terminaison amino sont des éthers polyoxydes allyliques dans lesquels l'extrémité hydroxyle est remplacée par un groupe amine.
37. Quels types de catalyseurs polyuréthane sont couramment utilisés ? Quelles variétés couramment utilisées sont incluses ?
A : Les catalyseurs d'amine tertiaire, les variétés couramment utilisées sont : triéthylènediamine, diméthyléthanolamine, n-méthylmorpholine, N, n-diméthylcyclohexamine
Les composés alkyles métalliques, les variétés couramment utilisées sont : les catalyseurs organostanniques, peuvent être divisés en octoate stanneux, oléate stanneux, dilaurate de dibutylétain.
38. Quels sont les allongeurs de chaîne ou agents de réticulation en polyuréthane couramment utilisés ?
A : Polyols (1, 4-butanediol), alcools alicycliques, alcools aromatiques, diamines, alcoolamines (éthanolamine, diéthanolamine)
39. Mécanisme de réaction des isocyanates
R : La réaction des isocyanates avec les composés à hydrogène actif est provoquée par le centre nucléophile de la molécule du composé à hydrogène actif qui attaque l’atome de carbone à base de NCO. Le mécanisme de réaction est le suivant :
40. Comment la structure de l'isocyanate affecte-t-elle la réactivité des groupes NCO ?
R : L'électronégativité du groupe AR : si le groupe R est un groupe absorbant les électrons, la densité du nuage électronique de l'atome C dans le groupe -NCO est plus faible et il est plus vulnérable à l'attaque des nucléophiles, c'est-à-dire qu'il il est plus facile d'effectuer des réactions nucléophiles avec des alcools, des amines et d'autres composés. Si R est un groupe donneur d'électrons et est transféré à travers le nuage électronique, la densité du nuage électronique de l'atome C dans le groupe -NCO augmentera, le rendant moins vulnérable à l'attaque des nucléophiles, et sa capacité de réaction avec les composés d'hydrogène actif augmentera. diminuer. B. Effet d'induction : Parce que le diisocyanate aromatique contient deux groupes NCO, lorsque le premier gène -NCO participe à la réaction, en raison de l'effet conjugué du cycle aromatique, le groupe -NCO qui ne participe pas à la réaction jouera le rôle du groupe absorbant les électrons, de sorte que l'activité réactionnelle du premier groupe NCO soit améliorée, ce qui est l'effet d'induction. C. effet stérique : Dans les molécules de diisocyanate aromatique, si deux groupes -NCO sont dans un cycle aromatique en même temps, alors l'influence d'un groupe NCO sur la réactivité de l'autre groupe NCO est souvent plus significative. Cependant, lorsque deux groupes NCO sont situés dans des cycles aromatiques différents dans la même molécule, ou qu'ils sont séparés par des chaînes hydrocarbonées ou des cycles aromatiques, l'interaction entre eux est faible et elle diminue avec l'augmentation de la longueur de la chaîne hydrocarbonée ou de la augmentation du nombre de cycles aromatiques.
41. Types de composés à hydrogène actif et réactivité NCO
A : NH2 aliphatique > Groupe aromatique Bozui OH > Eau > OH secondaire > Phénol OH > Groupe carboxyle > Urée substituée > Amido > Carbamate. (Si la densité du nuage électronique du centre nucléophile est plus élevée, l'électronégativité est plus forte, l'activité de réaction avec l'isocyanate est plus élevée et la vitesse de réaction est plus rapide ; sinon, l'activité est faible.)
42. Influence des composés hydroxylés sur leur réactivité avec les isocyanates
R : La réactivité des composés à hydrogène actif (ROH ou RNH2) est liée aux propriétés de R, lorsque R est un groupe attracteur d'électrons (faible électronégativité), il est difficile de transférer des atomes d'hydrogène, et la réaction entre les composés à hydrogène actif et Le sous-officier est plus difficile ; Si R est un substituant donneur d'électrons, la réactivité des composés à hydrogène actif avec NCO peut être améliorée.
43. A quoi sert la réaction de l'isocyanate avec l'eau
R : C’est l’une des réactions de base dans la préparation de la mousse de polyuréthane. La réaction entre eux produit d’abord un acide carbamique instable, qui se décompose ensuite en CO2 et en amines, et si l’isocyanate est en excès, l’amine résultante réagit avec l’isocyanate pour former une urée.
44. Lors de la préparation des élastomères polyuréthanes, la teneur en eau des polymères polyols doit être strictement contrôlée.
R : Aucune bulle n'est requise dans les élastomères, les revêtements et les fibres, la teneur en eau des matières premières doit donc être strictement contrôlée, généralement inférieure à 0,05 %.
45. Différences dans les effets catalytiques des catalyseurs à base d'amine et d'étain sur les réactions des isocyanates
R : Les catalyseurs d'amine tertiaire ont une efficacité catalytique élevée pour la réaction de l'isocyanate avec l'eau, tandis que les catalyseurs à l'étain ont une efficacité catalytique élevée pour la réaction de l'isocyanate avec le groupe hydroxyle.
46. Pourquoi la résine polyuréthane peut-elle être considérée comme un polymère séquencé et quelles sont les caractéristiques de la structure de la chaîne ?
Réponse : Étant donné que le segment de chaîne de la résine polyuréthane est composé de segments durs et mous, le segment dur fait référence au segment de chaîne formé par la réaction de l'isocyanate, de l'extenseur de chaîne et de l'agent de réticulation sur la chaîne principale des molécules de polyuréthane, et ces groupes ont une plus grande cohésion. énergie, un plus grand volume d’espace et une plus grande rigidité. Le segment souple fait référence au polyol polymère de la chaîne principale carbone-carbone, qui a une bonne flexibilité et constitue un segment flexible de la chaîne principale du polyuréthane.
47. Quels sont les facteurs qui affectent les propriétés des matériaux polyuréthane ?
A : Énergie de cohésion de groupe, liaison hydrogène, cristallinité, degré de réticulation, poids moléculaire, segment dur, segment mou.
48. Quelles matières premières sont les segments souples et durs de la chaîne principale des matériaux en polyuréthane
R : Le segment mou est composé de polyols oligomères (polyester, polyéther diols, etc.) et le segment dur est composé de polyisocyanates ou de leur combinaison avec des allongeurs de chaîne à petites molécules.
49. Comment les segments souples et les segments durs affectent-ils les propriétés des matériaux polyuréthane ?
A : Segment souple : (1) Le poids moléculaire du segment souple : en supposant que le poids moléculaire du polyuréthane est le même, si le segment souple est en polyester, la résistance du polyuréthane augmentera avec l'augmentation du poids moléculaire de le polyester diol ; Si le segment souple est du polyéther, la résistance du polyuréthane diminue avec l'augmentation du poids moléculaire du polyéther diol, mais l'allongement augmente. (2) La cristallinité du segment mou : Il contribue davantage à la cristallinité du segment de chaîne linéaire en polyuréthane. En général, la cristallisation est bénéfique pour améliorer les performances des produits en polyuréthane, mais parfois la cristallisation réduit la flexibilité du matériau à basse température et le polymère cristallin est souvent opaque.
Segment dur : Le segment de chaîne dure affecte généralement la température de ramollissement et de fusion ainsi que les propriétés à haute température du polymère. Les polyuréthanes préparés par des isocyanates aromatiques contiennent des anneaux aromatiques rigides, de sorte que la résistance du polymère dans le segment dur augmente et que la résistance du matériau est généralement supérieure à celle des polyuréthanes isocyanates aliphatiques, mais la résistance à la dégradation par les ultraviolets est faible et il est facile de jaunir. Les polyuréthanes aliphatiques ne jaunissent pas.
50. Classification de la mousse de polyuréthane
A : (1) mousse dure et mousse souple, (2) mousse haute densité et basse densité, (3) mousse de type polyester, mousse de type polyéther, (4) mousse de type TDI, mousse de type MDI, (5) mousse de polyuréthane et mousse de polyisocyanurate, (6) méthode de production en une étape et méthode de prépolymérisation, méthode continue et production intermittente, (8) mousse en bloc et mousse moulée.
51. Réactions de base dans la préparation de la mousse
R : Il fait référence à la réaction de -NCO avec -OH, -NH2 et H2O, et lors de la réaction avec des polyols, la « réaction de gel » dans le processus de moussage fait généralement référence à la réaction de formation de carbamate. Étant donné que la matière première de la mousse utilise des matières premières multifonctionnelles, un réseau réticulé est obtenu, ce qui permet au système moussant de se gélifier rapidement.
La réaction moussante se produit dans le système moussant en présence d’eau. La « réaction moussante » fait généralement référence à la réaction de l’eau et de l’isocyanate pour produire de l’urée substituée et libérer du CO2.
52. Mécanisme de nucléation des bulles
La matière première réagit dans un liquide ou dépend de la température produite par la réaction pour produire une substance gazeuse et volatiliser le gaz. Avec la progression de la réaction et la production d’une grande quantité de chaleur de réaction, la quantité de substances gazeuses et la volatilisation ont augmenté continuellement. Lorsque la concentration de gaz augmente au-delà de la concentration de saturation, une bulle soutenue commence à se former dans la phase de solution et monte.
53. Le rôle du stabilisant de mousse dans la préparation de la mousse de polyuréthane
R : Il a un effet émulsifiant, de sorte que la solubilité mutuelle entre les composants du matériau mousse est améliorée ; Après l'ajout d'un tensioactif silicone, parce qu'il réduit considérablement la tension superficielle γ du liquide, l'énergie libre accrue requise pour la dispersion gazeuse est réduite, de sorte que l'air dispersé dans la matière première est plus susceptible de se nucléer pendant le processus de mélange, ce qui contribue à la production de petites bulles et améliore la stabilité de la mousse.
54. Mécanisme de stabilité de la mousse
R : L’ajout de tensioactifs appropriés favorise la formation d’une dispersion de fines bulles.
55. Mécanisme de formation de mousse à cellules ouvertes et de mousse à cellules fermées
R : Le mécanisme de formation de la mousse à cellules ouvertes : dans la plupart des cas, lorsqu'il y a une forte pression dans la bulle, la résistance de la paroi de la bulle formée par la réaction du gel n'est pas élevée et le film mural ne peut pas résister à l'étirement provoqué. par la pression croissante du gaz, le film de la paroi à bulles est tiré et le gaz s'échappe de la rupture, formant la mousse à cellules ouvertes.
Mécanisme de formation de mousse à cellules fermées : pour le système à bulles dures, en raison de la réaction des polyéther polyols à faible poids moléculaire multifonctionnel et avec le polyisocyanate, la vitesse de gel est relativement rapide et le gaz dans la bulle ne peut pas briser la paroi de la bulle. , formant ainsi la mousse à cellules fermées.
56. Mécanisme de moussage de l'agent moussant physique et de l'agent moussant chimique
A : Agent gonflant physique : L'agent gonflant physique est que les pores de la mousse se forment par le changement de la forme physique d'une certaine substance, c'est-à-dire par l'expansion du gaz comprimé, la volatilisation du liquide ou la dissolution du solide.
Agents gonflants chimiques : les agents gonflants chimiques sont des composés qui, lorsqu'ils sont décomposés par la chaleur, libèrent des gaz tels que le dioxyde de carbone et l'azote et forment de fins pores dans la composition polymère.
57. Méthode de préparation de la mousse de polyuréthane souple
A : Méthode en une étape et méthode prépolymère
Méthode du prépolymère : c'est-à-dire que la réaction du polyéther polyol et de l'excès de TDI est transformée en un prépolymère contenant un groupe NCO libre, puis mélangée avec de l'eau, un catalyseur, un stabilisant, etc., pour produire de la mousse. Méthode en une étape : une variété de matières premières sont directement mélangées dans la tête de mélange par calcul, et une étape est constituée de mousse, qui peut être divisée en continue et intermittente.
58. Caractéristiques du moussage horizontal et du moussage vertical
Méthode de plaque de pression équilibrée : caractérisée par l’utilisation d’un papier supérieur et d’une plaque de couverture supérieure. Méthode de rainure de trop-plein : caractérisée par l'utilisation d'une rainure de trop-plein et d'une plaque d'atterrissage pour bande transporteuse.
Caractéristiques de moussage vertical : vous pouvez utiliser un petit débit pour obtenir une grande section transversale de blocs de mousse, et généralement utiliser une machine à mousse horizontale pour obtenir la même section du bloc, le niveau d'écoulement est 3 à 5 fois plus grand que le niveau vertical moussant; En raison de la grande section transversale du bloc de mousse, il n'y a pas de peau supérieure et inférieure, et la peau des bords est également fine, de sorte que la perte de coupe est considérablement réduite. L'équipement couvre une petite surface, la hauteur de l'usine est d'environ 12 à 13 m et le coût d'investissement de l'usine et de l'équipement est inférieur à celui du processus de moussage horizontal ; Il est facile de remplacer la trémie et le modèle pour produire des corps de mousse cylindriques ou rectangulaires, notamment des billettes de mousse rondes pour la découpe rotative.
59. Points de base de la sélection des matières premières pour la préparation de mousse souple
A : Polyol : polyéther polyol pour mousse en bloc ordinaire, le poids moléculaire est généralement de 3 000 à 4 000, principalement du polyéther triol. Le polyéther triol d'un poids moléculaire de 4 500 à 6 000 est utilisé pour la mousse à haute résilience. Avec l'augmentation du poids moléculaire, la résistance à la traction, l'allongement et la résilience de la mousse augmentent. La réactivité des polyéthers similaires a diminué. Avec l'augmentation du degré fonctionnel du polyéther, la réaction est relativement accélérée, le degré de réticulation du polyuréthane est augmenté, la dureté de la mousse est augmentée et l'allongement est diminué. Isocyanate : La matière première isocyanate de la mousse souple en polyuréthane est principalement le diisocyanate de toluène (TDI-80). L'activité relativement faible du TDI-65 n'est utilisée que pour la mousse de polyester polyuréthane ou la mousse de polyéther spéciale. Catalyseur : Les avantages catalytiques du moussage de mousse souple en vrac peuvent être grossièrement divisés en deux catégories : l'une concerne les composés organométalliques, le caprylate stanneux étant le plus couramment utilisé ; Un autre type est celui des amines tertiaires, couramment utilisées comme éthers diméthylaminoéthyliques. Stabilisateur de mousse : dans la mousse en vrac de polyester et de polyuréthane, des tensioactifs sans silicium sont principalement utilisés, et dans la mousse en vrac de polyéther, un copolymère d'oléfine organosilica-oxydé est principalement utilisé. Agent moussant : En général, seule l'eau est utilisée comme agent moussant lorsque la densité des bulles du bloc souple en polyuréthane est supérieure à 21 kg par mètre cube ; Les composés à bas point d'ébullition tels que le chlorure de méthylène (MC) sont utilisés comme agents gonflants auxiliaires uniquement dans les formulations à faible densité.
60. Influence des conditions environnementales sur les propriétés physiques des blocs de mousse
R : L'effet de la température : la réaction de moussage du polyuréthane s'accélère à mesure que la température du matériau augmente, ce qui entraînera un risque de brûlure du noyau et d'incendie dans les formulations sensibles. L'influence de l'humidité de l'air : Avec l'augmentation de l'humidité, en raison de la réaction du groupe isocyanate dans la mousse avec l'eau de l'air, la dureté de la mousse diminue et l'allongement augmente. La résistance à la traction de la mousse augmente avec l'augmentation du groupe urée. L'effet de la pression atmosphérique : Pour la même formule, lors d'un moussage à une altitude plus élevée, la densité est considérablement réduite.
61. La principale différence entre le système de matières premières utilisé pour la mousse souple moulée à froid et la mousse moulée à chaud
R : Les matières premières utilisées dans le moulage par durcissement à froid ont une réactivité élevée et il n'y a pas besoin de chauffage externe pendant le durcissement, en fonction de la chaleur générée par le système, la réaction de durcissement peut être pratiquement terminée en peu de temps et le moule peut être libéré quelques minutes après l’injection des matières premières. La réactivité des matières premières de la mousse de moulage durcissant à chaud est faible, et le mélange réactionnel doit être chauffé avec le moule après le moussage dans le moule, et le produit en mousse peut être libéré après avoir complètement mûri dans le canal de cuisson.
62. Quelles sont les caractéristiques de la mousse souple moulée à froid par rapport à la mousse moulée à chaud
R : ① Le processus de production ne nécessite pas de chaleur externe, peut économiser beaucoup de chaleur ; ② Coefficient d'affaissement élevé (rapport de repli), bonnes performances de confort ; ③ Taux de rebond élevé ; ④ La mousse sans ignifuge possède également certaines propriétés ignifuges ; ⑤ Cycle de production court, peut économiser du moule et réduire les coûts.
63. Caractéristiques et utilisations respectivement de la bulle molle et de la bulle dure
R : Caractéristiques des bulles molles : La structure cellulaire des bulles molles en polyuréthane est en grande partie ouverte. Généralement, il a une faible densité, une bonne récupération élastique, une absorption acoustique, une perméabilité à l'air, une conservation de la chaleur et d'autres propriétés. Utilisations : principalement utilisé pour les meubles, les matériaux de coussin, les matériaux de coussin de siège de véhicule, une variété de matériaux composites stratifiés à rembourrage souple, la mousse souple industrielle et civile est également utilisée comme matériaux filtrants, matériaux d'isolation phonique, matériaux antichoc, matériaux décoratifs, matériaux d'emballage. et des matériaux d'isolation thermique.
Caractéristiques de la mousse rigide : la mousse de polyuréthane est légère, a une résistance spécifique élevée et une bonne stabilité dimensionnelle ; Les performances d’isolation thermique de la mousse rigide de polyuréthane sont supérieures. Forte force adhésive ; Bonnes performances de vieillissement, longue durée de vie adiabatique ; Le mélange réactionnel a une bonne fluidité et peut remplir en douceur la cavité ou l'espace de forme complexe. La matière première de la production de mousse dure de polyuréthane a une réactivité élevée, peut obtenir un durcissement rapide et peut atteindre un rendement élevé et une production de masse en usine.
Utilisations : utilisé comme matériau d'isolation pour les réfrigérateurs, les congélateurs, les conteneurs réfrigérés, les entrepôts frigorifiques, l'isolation des oléoducs et des conduites d'eau chaude, l'isolation des murs et des toits des bâtiments, les panneaux sandwich isolants, etc.
64. Points clés de la conception de la formule à bulles dures
R : Polyols : les polyols de polyéther utilisés pour les formulations de mousse dure sont généralement des polyols d'oxyde de polypropylène à haute énergie et à valeur d'hydroxyle élevée (faible poids moléculaire) ; Isocyanate : À l'heure actuelle, l'isocyanate utilisé pour les bulles dures est principalement le polyisocyanate de polyméthylène polyphényle (généralement connu sous le nom de PAPI), c'est-à-dire le MDI brut et le MDI polymérisé ; Agents gonflants : (1) agent gonflant CFC (2) agent gonflant HCFC et HFC (3) agent gonflant pentane (4) eau ; Stabilisateur de mousse : Le stabilisant de mousse utilisé pour la formulation de mousse rigide de polyuréthane est généralement un polymère séquencé de polydiméthylsiloxane et de polyoxoléfine. À l'heure actuelle, la plupart des stabilisants de mousse sont principalement de type Si-C ; Catalyseur : Le catalyseur de la formulation à bulles dures est principalement une amine tertiaire, et le catalyseur organostannique peut être utilisé dans des occasions spéciales ; Autres additifs : Selon les exigences et les besoins des différentes utilisations des produits en mousse rigide de polyuréthane, des retardateurs de flamme, des agents d'ouverture, des inhibiteurs de fumée, des agents anti-âge, des agents anti-moisissure, des agents de renforcement et d'autres additifs peuvent être ajoutés à la formule.
65. Principe de préparation de la mousse de moulage de peau entière
R : La mousse à peau intégrale (ISF), également connue sous le nom de mousse auto-écorchée (mousse auto-écorchée), est une mousse plastique qui produit sa propre peau dense au moment de la fabrication.
66. Caractéristiques et utilisations des élastomères microporeux polyuréthanes
R: Caractéristiques: l'élastomère polyuréthane est un polymère séquencé, généralement composé d'un segment souple à longue chaîne flexible de polyol oligomère, d'un diisocyanate et d'un prolongateur de chaîne pour former un arrangement alternatif de segment dur, de segment dur et de segment mou, formant une unité structurelle répétitive. En plus de contenir des groupes ester d'ammoniac, le polyuréthane peut former des liaisons hydrogène à l'intérieur et entre les molécules, et les segments mous et durs peuvent former des régions de microphase et produire une séparation de microphase.
67. Quelles sont les principales caractéristiques de performance des élastomères polyuréthanes
R : Caractéristiques de performance : 1, haute résistance et élasticité, peut être dans une large gamme de dureté (Shaw A10 ~ Shaw D75) pour maintenir une élasticité élevée ; Généralement, la faible dureté requise peut être obtenue sans plastifiant, il n'y a donc aucun problème causé par la migration du plastifiant ; 2, sous la même dureté, capacité de charge plus élevée que les autres élastomères ; 3, excellente résistance à l’usure, sa résistance à l’usure est 2 à 10 fois supérieure à celle du caoutchouc naturel ; 4. Excellente résistance à l’huile et aux produits chimiques ; Polyuréthane aromatique résistant aux radiations ; Excellente résistance à l'oxygène et à l'ozone ; 5, résistance élevée aux chocs, bonne résistance à la fatigue et résistance aux chocs, adaptée aux applications de flexion à haute fréquence ; 6, la flexibilité à basse température est bonne ; 7, le polyuréthane ordinaire ne peut pas être utilisé au-dessus de 100 ℃, mais l'utilisation d'une formule spéciale peut résister à une température élevée de 140 ℃ ; 8, les coûts de moulage et de traitement sont relativement faibles.
68. Les élastomères de polyuréthane sont classés selon les polyols, les isocyanates, les procédés de fabrication, etc.
R : 1. Selon la matière première du polyol oligomère, les élastomères de polyuréthane peuvent être divisés en type polyester, type polyéther, type polyoléfine, type polycarbonate, etc. Le type polyéther peut être divisé en type polytétrahydrofurane et type oxyde de polypropylène selon des variétés spécifiques ; 2. Selon la différence du diisocyanate, il peut être divisé en élastomères aliphatiques et aromatiques, et subdivisé en type TDI, type MDI, type IPDI, type NDI et autres types ; Depuis le processus de fabrication, les élastomères polyuréthanes sont traditionnellement divisés en trois catégories : type coulé (CPU), thermoplasticité (TPU) et type mélange (MPU).
69. Quels sont les facteurs affectant les propriétés des élastomères polyuréthanes du point de vue de la structure moléculaire ?
R: Du point de vue de la structure moléculaire, l'élastomère de polyuréthane est un polymère séquencé, généralement composé d'oligomères polyols, d'un segment souple à longue chaîne flexible, d'un diisocyanate et d'un prolongateur de chaîne pour former un arrangement alternatif de segment dur, de segment dur et de segment mou, formant un agencement répétitif. unité structurelle. En plus de contenir des groupes ester d'ammoniac, le polyuréthane peut former des liaisons hydrogène à l'intérieur et entre les molécules, et les segments mous et durs peuvent former des régions de microphase et produire une séparation de microphase. Ces caractéristiques structurelles confèrent aux élastomères de polyuréthane une excellente résistance à l'usure et une excellente ténacité, connue sous le nom de « caoutchouc résistant à l'usure ».
70. Différence de performances entre les élastomères de type polyester ordinaire et les élastomères de type polytétrahydrofurane éther
R : Les molécules de polyester contiennent des groupes ester plus polaires (-COO-), qui peuvent former de fortes liaisons hydrogène intramoléculaires, de sorte que le polyester-polyuréthane a une résistance élevée, une résistance à l'usure et une résistance à l'huile.
L'élastomère préparé à partir de polyols de polyéther présente une bonne stabilité à l'hydrolyse, une bonne résistance aux intempéries, une flexibilité à basse température et une bonne résistance à la moisissure. Source de l'article/Recherche sur l'apprentissage des polymères

Heure de publication : 17 janvier 2024